What’s the litmus test for Smart Factory
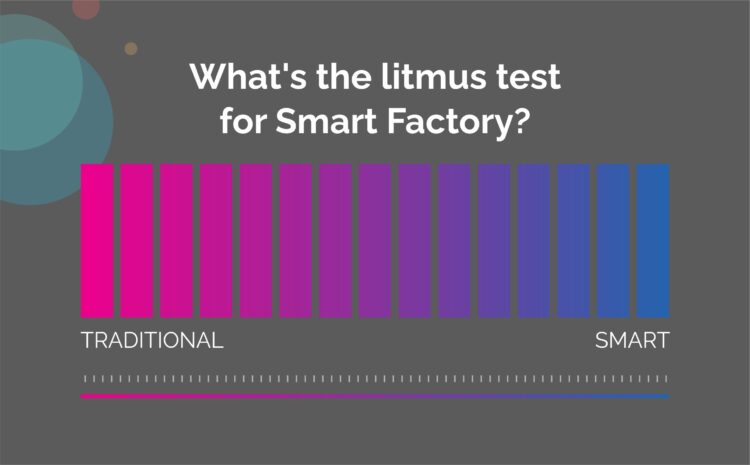
So, when exactly does a factory be termed as smart?
The short answer is never. Because it’s an ongoing process.
Smart Factory is not a destination but a journey. However, there are several indicative situations in this journey that can be marked as progress towards becoming smarter in manufacturing. Each shift in hue signals a milestone reached, guiding you towards smart manufacturing and excellence.
Most team meetings have ‘improvement’ on their agenda.
Change in meeting agendas is the first step. Meetings are not for sharing information, asking each other for data, or not even for making decisions based on the information. Once most of the meetings start and end with driving improvement as their primary agenda, be assured that your factory is turning smarter. For instance, at Sigma Toolings it’s almost 3 years since we have had a meeting to discuss who missed the production target and why? When we gather, everyone is already aware about it and we only discuss how the repetition can be avoided or the process can be improved, with production planning modified in the future. The teams take the color of change.
Data is available in real-time and most processes begin to be automated.
If junior teams have stopped spending hours and days together to gather the data and prepare reports, it’s a strong indicator that the processes are smart. If relatively senior teams have stopped asking for data and get the inputs for decision making in real time, the factory is turning smart. At Sigma, most of our reporting is automated. And there is traction to automate more and more processes.
Radical and rapid change is the new norm in the organisation.
If your team says yes to the question ‘Can we reduce hour delivery time by half’, in the next few days, they feel empowered. A clear indicator that your factory is smarter. If they indeed reduce the delivery time by half, it’s a reality. And if after 3-4 months, they are again ready to half the delivery time further, it’s progress. If the team is confident and ready to take bold steps for significant change, not marginal, it’s evident that your factory is smart. At Sigma, in the past 6 months, we have reduced cycle times by 90% and also significantly brought down the delivery times. This is after a similar such result just a few months ago. There is always room for significant improvement. We just need to aim higher!
Transparency becomes visible.
Yes! If the supervision, monitoring, management, middle layers become less and less or totally redundant, the factory is fast becoming smart. At Sigma, all our Operators have gained supervisory capabilities. Equipped with a tab, where they fill in all the production data, analyse their workload and respond in real-time with their decisions. So, at Sigma, we don’t have Operators anymore as all of them have taken up the responsibility as ‘Working Supervisors’. They are aware of their targets, know what they have achieved and how that’s linked to their financial appraisal. They understand how they score and are rated by the system, and trained and encouraged to improve their performance for growth. Also, Sigma has a 3600 Performance Review, where all working supervisors rate their colleagues including seniors.
While there could definitely be a few more additions to this list, the situations above are a great starting point in testing whether your factory is turning smart.
Got doubts? I will be happy to share thoughts on early, mid or advanced stage evaluation of your smart factory initiatives.
Get in touch at abhishek@sigmatoolings.com to fix an appointment.